製造現場のデジタル化をどう進める?ー後編ー
「スマートファクトリープロジェクト」で目指したもの
→製造現場のデジタル化をどう進める?ー前編ーはこちらからご覧いただけます。
新たな展開を生み出した新システムの運用が、世界規模での可能性を広げていく
DELMIA Apriso(デルミアアプリソ 以下 Apriso)導入へと動き出したコベルコ建機株式会社様。
実際にシステムの運用を開始して、作業工程のデータを一元管理して他のデータとつなぎ合わせることで、
それまで見えなかった情報を数値で見ることができるようになりました。
このような国内工場での成功体験を海外工場にも展開していく新たなビジョンを目指して取り組みを継続しているそうです。
そして、現場の作業員とのコミュニケーションを密に行い、現場が欲しいデータを共有し、オペレーショナルKPIとして可視化することにより、効果につながる具体的な作業工程の改善を行うことが可能になったそうです。
こういった成果が評価され、Apriso導入は国内の他工場へも広がることとなりました。
システム導入を主導してきた宍戸義昭さんにお話を伺いました。
グローバルITシステム部 担当部長
兼DXシステムグループ グループ長
宍戸義昭さんと
KIS川崎
たかが2分、されど2分。製造工程と品質管理の効率化が評価され、他工場でもApriso導入が決定
――― Apriso導入により得られたデータを活用した改善活動によって、
生産ラインの編成効率を向上させる取り組みにつながったというお話でしたが、
具体的にどのような変化が生まれたのでしょうか?
宍戸 生産ラインの各作業者の標準作業手順を定着させるプロジェクトにおいて、Apriso導入で得られた各作業者の作業着手から完了までの実績時間を活用し、生産ラインの工程数を増やす設備投資を行い、作業編成を見直しました。
以前は広島事業所の五日市工場の組立ラインにおいては1台当たり約15分のサイクルタイムでの生産が限界だと思っていましたが、今ではサイクルタイム13分以下に短縮できる実力がつきました。
これはとても大きな成果で、我々としては壁を突破したという実感があります。
たった2分の時間短縮というような印象を受けるかもしれませんが、生産ラインの作業員の人数が仮に100人とすると、これら全員分の作業時間の合計は200分となり、時間あたりの作業チャージをかけると1台当たり約3万円、年間約3億円の原価削減が可能となる計算となります。
これは、生産ラインの可視化により顕在化した課題に対し、具体的な解決策を現場のみなさんが取り組んでくれたからこそ実現できたことであり、Aprisoのデータ活用と現場改善の行動力の両輪が嚙み合ったからこそ実現できたことと感じています。
―――Aprisoと現場の連携で業務が改善され、成果が上がったのですね。
品質管理の向上も導入前の課題に上がっていましたが、そちらも効果はありましたか?
宍戸 品質管理や品質問題が市場で発生した時の対応スピードの面でも効果がありました。
以前は、市場において製品の品質問題が発生した際、品質保証部門は、品質問題が発生した個体の生産記録を確認したり、問題が発生した部品が既に販売したどの個体に装着されているかを確認し同一の問題が発生しているか否かを迅速に確認する必要がありました。
このような確認を従来の仕組みでは複数のシステムやエクセルファイルにより行う必要があり、ひとつの案件で約1週間確認作業がかかることもありました。
また、関連システムの操作やデータ構造を熟知している人材も限定的で、情報確認作業の負荷は特定の人に集中していました。
今はAprisoに必要なデータは全て関連付けられ一元管理されているため、5分もあればパっと必要なデータが確認でき、Aprisoさえ使えれば担当者各自で対応可能となったため、品質問題の対応スピードが格段に向上しました。
それから、性能検査を自動化してデータを可視化していることで、現場での品質改善も向上しています。
例えば、油圧ショベルの場合、圧力センサーで油圧回路の圧力管理箇所を計測した数値がAprisoに集積されています。
ダッシュボード上で圧力の計測値を時系列で追いかけられるので、もしも計測値が中央値から外れる傾向が見られたら、その原因を突き止めて中央値に戻すようにする、というふうに品質管理への活用もできるようになりました。
―――なるほど。製造工程で見えなかったものをデータ化して「可視化」することで
いろんな可能性が広がっているのですね。
宍戸 そうですね。
―――コベルコ建機さんでは新しい取り組みを行うに際して「スモールスタート」を行なっているそうですが、
Aprisoの導入は他の工場へも広がっていますか?
宍戸 弊社では工場ごとにシステムを導入、検証し、成果が出れば段階的に他工場へも導入しています。
Aprisoは広島(五日市工場)に続きミニショベルを製造している岐阜(大垣工場)でも同じシステムを導入しました。
兵庫(大久保工場)ではクレーンを製造していますが、一部でAprisoを導入しています。
海外では、中国、タイ、インドで性能検査を導入予定でしたが、コロナ感染症の影響で延期中です。
今後、コロナ感染症が収束すれば導入に向けた検討も行われると思います。
成功の鍵はコミュニケーション。ベンダーや現場との連携によってスムーズな導入が実現
―――それでは、少し現場でのお話を聞かせてください。
新システム導入に際しては様々な変化と共にトラブルも起こるのではないかと思いますが、
どのようなご苦労があったでしょうか?
宍戸 システム構築に際しては、あまり苦労はなかったと思います。
機器やデバイス、シーケンサーとつなぐところのエンジニアが絶対的に少なく、その辺りの接続やインターフェイスへの対応などは大変だったところもありましたが、そこは担当していたコベルコシステムが強かったので対処できました。
―――(Apriso)導入プロジェクトはスムーズに進んだのですね。
宍戸 そうですね。
工程はステップ分けして進めて、約1年で完成しました。
のちにいろいろな機能を追加して改良しながら現在に至っています。
―――現場の反応はいかがだったでしょうか?
実際に作業に当たられる製造現場の方々は、
慣れたやり方から新しいやり方に変わることに抵抗はありませんでしたか?
宍戸 弊社にはスタッフと現場が一緒になってやる社風があって、風通しが良い会社なので、新しいシステム導入に関して現場の抵抗はそれほどありませんでした。
最初は手間が増えるという声もあったようですが、担当者が丁寧に製造現場の方に説明してくれて。
みんなで話し合い、手間が少し増えるが、良くなる点もたくさんあることを理解、納得してもらいました。
全拠点を繋ぐ「グローバル品質トレーサビリティシステム」の実現へ
―――今までのお話から、Aprisoの導入によって抱えていた課題が解決されただけでなく、
製造工程や品質管理の効率化も実現され、成果につながったということがよくわかりました。
宍戸さんは次のステップとしてどんなことを考えていらっしゃいますか?
今後のビジョンを教えてください。
宍戸 私はスマートファクトリーの推進は今後も重要になってくると考えているので、Aprisoを全工場に展開していきたいと思っています。
それからAprisoにより日本だけでなく海外拠点も含めた「グローバル品質トレーサビリティシステム」の構築をするべきと考えています。
現在、我々は現行ERPの2025年問題(2025年に現行のERPシステムのサポート期限が終了するため新システムへの移行が必要)に直面しています。
グローバルに展開している全拠点においてERPシステムを刷新中ですが、多くのアドオン機能開発をしていたことがシステム運用の足かせになっていて、現システムをアップデートしようと思ってもアドオン機能が邪魔してできない状態になってしまいました。
ですから、次のERPシステムではアドオン機能開発を最小限にするという方針を立てています。
しかしそうはいっても、やりたいことや現場の要望があるので、そこはMES(Apriso)でカバーできるようにしたいと思っています。
EPRとMES(Apriso)の機能配置を整備して、ERPの刷新とともにAprisoを展開していこうと構想中です。
ERPと MES(Apriso)の連携イメージ
もうひとつは、ダッソー・システムズさんの「3DEXPERIENCE Platform」(※)の導入を構想しています。
2D図面をなくして全てを3Dデータで繋げていき、3DEXPERIENCE PlatformとAprisoを連携させて「3Dワークインストラクション(3Dの作業指示書)」を現場で見られるようにしたいと思っています。
※設計、製造、サービスいたる開発プロセス全体に必要なデータを管理する共通の統合環境。
設計/解析に必要なデータが同じデータベースで管理され、ファイルの受け渡しを行うことなくシームレスに業務を進めることができ、開発プロセスに関わる全てのユーザーが3DEXPERIENCE Platformで共同作業ができるようになる。
3Dワークインストラクションイメージ
CADや全てのデータが3Dになるとデータ容量が大きくなり、技術的課題、量的課題が出てきますので、5~6年程度必要になると思いますが、ぜひ実現したいですね。
「3DEXPERIENCE Platform」はまだ世界でも導入実現しているところが少ないのですが、元々2016年の「スマートファクトリープロジェクト」で構想していたことなので、ぜひ弊社でやり抜きたいと思っています。
Aprisoはダッソー・システムズの製品ですので、当然3DEXPERIENCE Platformとの相性もいいですし、生産工程管理で確かな成果を出してくれているので、導入効果を期待しています。
海外工場での活用に向けて
KIS ダッソー・システムズさんは「最も成長する会社Global 100のNo.1」に選ばれたこともある、持続可能性があり成長が見込めると評価された世界のトップ企業。
ダッソー・システムズの「3Dエクスペアリエンスプラットフォーム」は共通のプラットフォームを作ってそこにいろんなシステムをのせていき、データの連携をとって情報を繋げていくというシステムです。
国内でも実現しているところはないし、世界でもまだ少ない最先端領域ですが、ダッソー・システムズさんのコンセプトと宍戸さんのビジョンが同じ方向を見ていて、考え方が一致しているからこそ、宍戸さんはそれを実現しようと動かれているのですね。
―――コベルコ建機さんでは世界的な先端システムの導入を目指していらっしゃるのですね。
KISもパートナーとして一緒に取り組んでいますが、今後の期待や要望としてはどんなことがありますか?
宍戸 KISさんには本当によくやっていただいていると思っています。
なので、特に要望はないのですが…。
強いていうなら、海外展開の時に一緒に行ってくれませんか?(笑)。
広島で構築したシステムをぜひ海外でも導入していきたいので、その時はよろしくお願いします。
KIS ありがとうございます。こちらこそよろしくお願いします。
<KIS’s eye>
コベルコ建機さんはいいものを効率的に作るという日本のものづくりの精神に溢れていて、同業他社さんの工場見学を受け入れるなど日本のリーディングカンパニーとして常に進化されています。
KISとしてもそんな素晴らしい方々と一緒にお仕事させていただけるのを大変ありがたく感じています。
引き続きよろしくお願いいたします。
ソリューションの詳細はこちら→次世代型グローバルMES「DELMIA Apriso」
お問い合わせはこちら→お問い合わせフォーム
企業DATAコベルコ建機株式会社
〒141-0001東京都品川区北品川5丁目5番15号(大崎ブライトコア5F)
https://www.kobelcocm-global.com/jp/
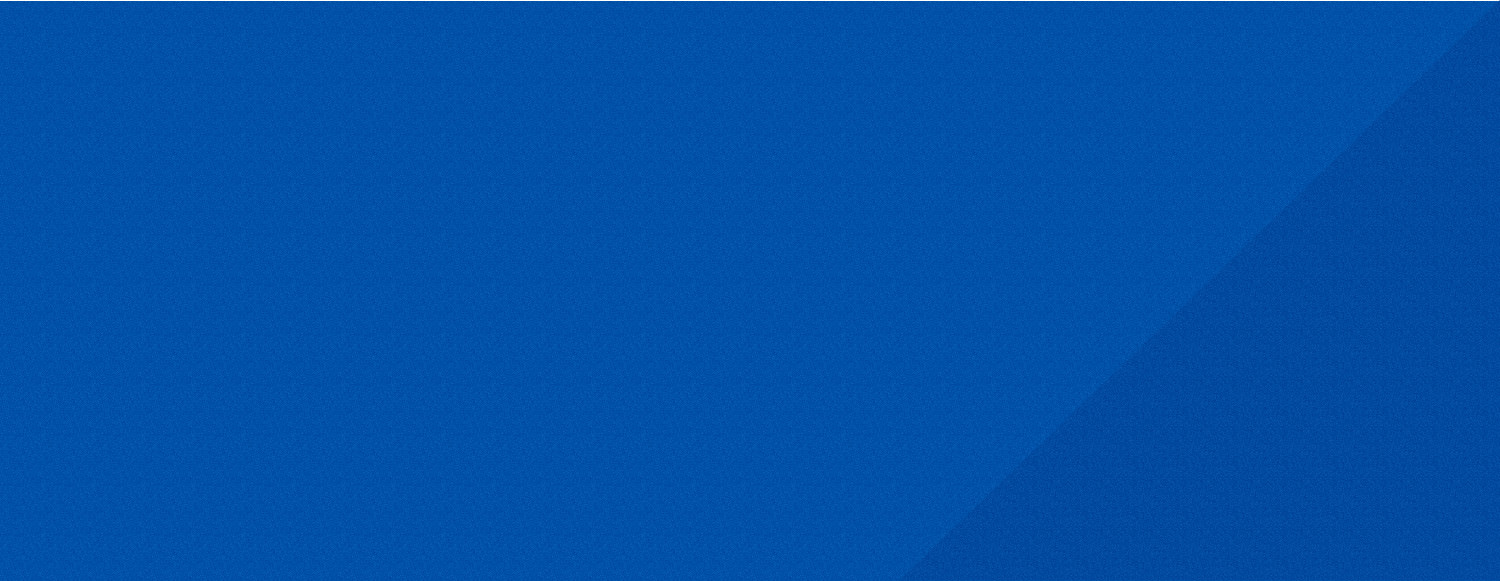