製造現場のデジタル化をどう進める?ー前編ー
「スマートファクトリープロジェクト」で目指したもの
デジタル化と効率化の秘訣は自社にマッチしたシステムを手に入れること
油圧ショベルとクレーンの製造を行い、海外にも生産拠点を置いて
グローバルな展開を行っているコベルコ建機株式会社様。
事業のグローバル化と販売台数の増加、その需要に対応するための生産拠点の増加に伴い
当然のように製品に関する生産工場の管理情報も増えていきますが、
商品需要の変化に応じて多品種変種変量のフレキシブルな生産を行っている製造現場では、
さらなる編成効率向上を目指す上で大きな壁にぶつかっていました。
「やらなければならないことはわかっているが、時間がかかりすぎて手がつけられない」
そんな悩みを抱えていた時に出会ったのが
次世代グローバルMES「DELMIA Apriso(デルミアアプリソ 以下Apriso)」。
自社のものづくりに適したシステムを、
柔軟性と開発効率の高さ、
安定したパフォーマンスで実現してくれるAprisoとの出会いは、
それまで越えられなかった壁を越える突破口になったそうです。
導入の決め手になったのは何だったのでしょうか?
システム導入を主導してきた宍戸義昭さんにお話を伺いました。
グローバルITシステム部 担当部長
兼 DXシステムグループ グループ長
宍戸義昭さん
製造現場のデジタル化をどう進める? 「スマートファクトリープロジェクト」で目指したもの
―――Aprisoの導入は2016年に着手されたとのことですね。
導入のきっかけについて教えていただけますか?
宍戸 2015年に2016年から2020年の中期計画を策定したのですが、
その頃はちょうど「インダストリー4.0」など製造業でデジタル化の推進が言われ始めた時期でした。
我々の周りでも「スマートファクトリー」などのキーワードが広まってきていて、
私はこの世の中の流れについていけないと弊社は取り残されてしまうという危機感を感じていました。
この波に乗らなければ競争力を失うだろうと思ったのです。
当時の経営陣も同じ見解だったため、社の方針がデジタル化推進でまとまり、
5年間に渡る「スマートファクトリープロジェクト」が策定されました。
Aprisoの導入はその中のひとつとして私が担当し推進したものでした。
コベルコ建機の商品は、大きく分けると油圧ショベルとクレーンのふたつに分類されます。
当時私が担当していた広島(五日市工場)では油圧ショベルを製造しており、その製造工程管理にAprisoを導入しました。
―――デジタル化の推進が始まったタイミングだったのですね。
当時、現場ではどのような課題があったのでしょうか?
また、改善しなければいけなかったのはどんなことでしたか?
宍戸 当時、弊社の製造現場では作業員が品質検査結果を紙に書いて記録していました。
それをエクセルに入力していたのですが、読めない文字や入力間違いなどがあって正確なデータがとれていなかったのです。
さらにそのデータがあちこちに分散していました。
もしも品質に問題が起きた場合、原因特定のために製品の製造過程に関する情報を集めて因果関係を調べるのですが、データがまとまっていない状態だったので原因を特定するまでに非常に時間がかかっていました。
ですから、品質問題への対応を早めるためには生産工場における情報管理体制の根本的な再構築が必要だったのです。
製造過程の生産記録をデジタル化、可視化して、
製品に関わる正確なデータをいつでも見られる状態にしておくことが急務となっていました。
―――製造過程のデータのデジタル化と情報の集約が課題の1つだったのですね。
その他にはどのような課題があったのでしょうか?
宍戸 当時、広島(五日市工場)では油圧ショベルを1日に40〜50台、月に1000台ほど生産していました。
製品は7t〜35tまで様々な大きさと仕様があり、製造過程ではコンベアラインに製品のフレームを流して順番に組み立てていきます。
弊社では、同じラインでいろいろな機種と仕様を製造する多品種混流生産を採用しています。
これは、ひとつのラインで複数の製品を作ることで製品の需要の変動に細やかに対応できるというメリットを重視しているためです。
しかし、この仕組みには課題もありました。
ひとつのコンベアラインにひとつの機種、ではなく複数の機種を流して製造していくので、
機種ごとに作業内容が変わり、作業員ひとりひとりの作業量の平準化が難しくなっていました。
詳しくお話しすると、
大きさ、重さの違うものを同じラインで流すと、製品によって工数や作業員一人あたりの作業分担量が違うため、
各工程の作業を全員が同じ時間で終えられなくなってしまいます。
その結果、作業時間がかかる工程がボトルネックとなって全体の製造時間が長くなっていたのです。
それを解決して編成効率を上げるためには作業の平準化が必要でしたが、
たくさんある作業工程のひとつひとつを検証していくには膨大な時間がかかるため簡単には着手できず、
どの作業にどれくらい時間がかかるか、どこを改善すればよいのかがわからない状況にありました。
例えば、1台の製品で全作業者の作業時間をストップウォッチで計測していくと、
全作業工程を把握するのに1機種あたり2ヶ月はかかります。
それを全機種に渡って計測・分析し、さらに工程を変更していくとなると膨大な時間がかかってしまいます。
そのため改善できないままでした。
しかし、これを解決しないと問題がなくならない。
ですから、作業の状況を可視化して、常日頃から作業分配を見直す取り組みをできるように
生産の実績情報の管理体制を変えていきたいと考えていました。
安定したパフォーマンスとカスタマイズ性能を持ち合わせたAprisoの魅力
―――そんな課題を解決するためにAprisoを導入されたわけですが、
どんなところが決め手になったのか、Aprisoを選ばれた経緯をお聞かせいただけますか?
宍戸 2016年にスマートファクトリープロジェクトを立ち上げる時、お付き合いのあったシステムベンダーさんに相談したところ、1からオリジナルのシステムをつくるスクラッチ開発を提案されました。
しかし弊社の状況には合っていないと感じていたので採用せず、
他にもいくつかの企業さんから提案を受けながらどうしようかと考えていた中で、
最終的にAprisoに決定しました。
――Aprisoを選ばれた理由を教えてください。
宍戸 Aprisoはスクラッチ開発とパッケージ製品の両方の長所を持っていることがとても良いと思いました。
Aprisoは作り上げられたデータモデルとビジネスコンポーネントを使って
自社の工程をプロセスビルダーで定義することができます。
標準機能を利用することで比較的プログラムレスで自社のモノづくりにあった製造実行システムを構築できる仕組みだったのです。
このコンセプトがとてもよいと思いました。
スクラッチで全部作るのは大変だし、完全パッケージでは自分達のものづくりにとって最適なものはできない。
Aprisoは両者の良いところを活かしたつくりだと思ったのです。
でもそれだけではまだ決めていなくて(笑)。
国内での製造業での導入実績を調べたり、
ダッソー・システムズさんの紹介で実際にAprisoを導入している会社を訪問して運用状況を聞いたりしました。
その結果、サポート体制も非常に手厚いこと、
トラブルもほぼなく安定しているということもわかり、導入を決めました。
―――なるほど。Aprisoは安定性がある上に自分達にあったカスタマイズもできるシステムだったんですね。
宍戸さんにはAprisoにピンとくるものがあったのですね?
宍戸 ありましたね!それでAprisoに決めました。
いよいよ新システム導入へと邁進
―――導入システムが決まったら、次は導入作業を担ってくれるベンダー探しになりますね。
KISとのご縁はどのように始まったのですか?
宍戸 ダッソー・システムズさんにコベルコ建機のシステムをお任せしているコベルコシステムとつながりがあり、腕が良くて信頼できて良心的、値段も良心的、人間性もいい、そんな感じでお願いして(笑)。
弊社の社風と相性が良さそうなところを、とお話をして紹介していただいたのがKISさんでした。
課題解決のための3つの軸
―――そうしてMES(Apriso)導入プロジェクトが始まったのですね。
それにあたってどんなことを重視していたのでしょうか?
先程伺った課題をどのように改善したのかを教えていただけますか?
宍戸 改善したかったのは、品質記録、編成効率(作業状態の可視化)、性能検査の3点でした。
① 品質記録のペーパーレス化
紙をなくして検査記録をAprisoに入力することで、製品に関する全ての情報がAprisoに集まるようにしました。
作業員は作業員IDの読み込み、作業のチェック記入、部品番号のシリアルQRをスキャンしています。
そうやって取得したデータを全てApriso上で管理することで、
作業工程の情報を製品の製造シリアルと紐づけられるようになっています。
このようにデータ同士が繋がっていくことで、品質の検証作業が容易になっています。
② 作業状態の可視化による編成効率のアップ
Aprisoの導入で全製造オーダーの全作業者の記録が蓄積されるようになりました。
作業に当たっている全作業者には、製造オーダーのバーコードと作業者IDをスキャンして読み込み、
Apriso画面上の作業着手ボタンを押してから作業を開始、終わったら完了ボタンを押すようにお願いしています。
そうすることで作業の工数差がデータで見えるようになりました。
さらに生産ラインの全工程の作業平準化を実施することで製造のピッチタイムを短くすることができました。
Apriso導入によって、スピードをもって編成効率のアップに取り組めるようになったと思います。
③設備連携による性能検査の信頼度向上
当時、社の方針として検査結果を完全に自動化しなさい、
検査した結果をデジタルデータで管理しなさいと大号令がかかりました。
すでにAprisoでの作業時間の記録、品質記録のペーパーレス化を実施していたタイミングだったので、
さらにAprisoと自動検査機器や検査デバイスをOPC-UA規格で連携させてこれを実現しました。
Aprisoから自動検査機器に基準値や検査方法を指示し、検査結果を基準値と突き合わせます。
検査に合格すれば次の工程に進め、NGならば原因を突き止めてこれを是正、
再検査に合格したら次の行程に進めるという仕組みを作り、品質管理の新しい体制を整えました。
この課題については約6か月間というスピード感で展開できました。
この展開の早さはAprisoという基盤が既にあったからだと思っています。
広島(五日市工場)でのこの試みは、グループの中でも見本となるような早い取り組みでした。
現在はそれを他の工場に展開しています。
海外の工場にも導入したかったのですが、コロナの影響でまだできていないのが残念なところですね。
では、実際にAprisoを導入してどんな効果が生まれたのでしょうか?
詳しくは後編をご覧ください。
ソリューションの詳細はこちら→次世代型グローバルMES「DELMIA Apriso」
お問い合わせはこちら→お問い合わせフォーム
企業DATAコベルコ建機株式会社
〒141-0001東京都品川区北品川5丁目5番15号(大崎ブライトコア5F)
https://www.kobelcocm-global.com/jp/
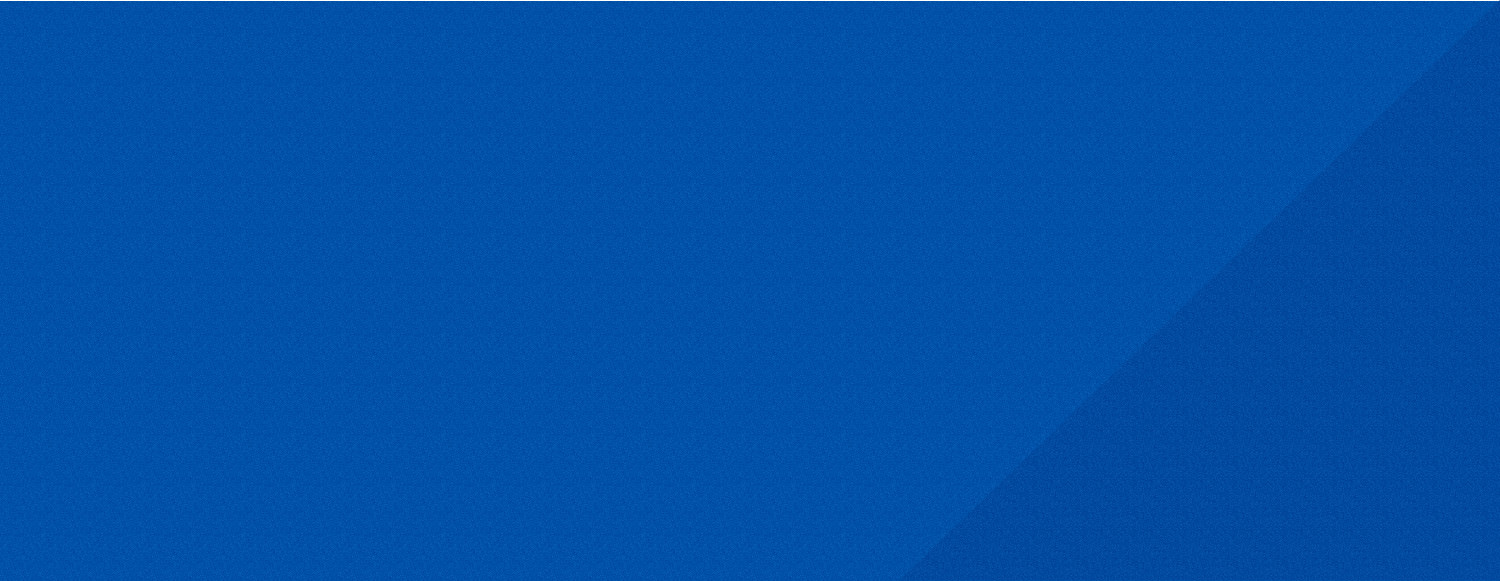